Kandıra Taşı
KANDIRA TAŞININ YAPI VE ÖZELLİKLERİ
Akın AKINCI
Sakarya Üniversitesi, Müh. Fak., Metalurji ve Malzeme Müh. Böl.,
Esentepe Kampüsü, 54187 Adapazarı, e-mail: akinci@sakarya.edu.tr
ÖZET
Kocaeli/Kandıra ilçesi sınırları içerisinde, ilçenin batı bölgesinden çıkartılan krem-bej ve gri-beyaz renklerdeki doğal taşın adı, literatürde ve ticari piyasada Kandıra Taşı olarak yer almaktadır. Kullanım alanları, tüm iç ve dış mekanlarda giderek artan bir hızla yaygınlaşmaktadır. Bu doğal taş malzeme, duvar kaplaması, heykel, barbekü, şömine ve parke taşı vb. olarak kullanılmaktadır.
Bu çalışmada, Kandıra taşının mekanik, fiziksel ve kısmen kimyasal özellikleri incelenmektedir. Kandıra taşının yapı ve özelliklerinin malzeme mühendisliği açısından belirlenmesi konusunda yapılan bu ilk çalışma, daha sonraki aşamalarda taşın ulusal/uluslararası standardizasyonu konusunda yapılacak çalışmalara ve diğer teorik/deneysel araştırmalara referans olacaktır. Bununla birlikte, elde edilen veriler ışığında kullanım alanlarının arttırılması, seri üretimi ve ihracatının geliştirilmesi konusunda yapılacak incelemelere de ışık tutması amaçlanmıştır.
Anahtar Kelimeler: Kandıra taşı, yapı, mekanik, fiziksel ve kimyasal özellikler
1. GİRİŞ
Yapıtaşlarında aranan genel özellikler; özgül ağırlığı minimum 1,8 gr/cm3 olmalı, patlayıcılar uygulandığında kolay parçalanmalı, atmosfere ve diğer mekanik etkilere dayanıklı olmalı, sağlığı etkileyecek radyoaktif içerikler taşımamalı, dağılabilen lifler ve kükürt içermemeli, güneşten veya kızdırıcı diğer faktörlerden etkilenen opal gibi sulu serbest silika veya zeolit mineralleri taşımamalıdır.
Killi ve oolitik kireçtaşları, travertenler, kumtaşları gibi tortullar ile andezitler ve çeşitli tüfler gibi volkanikler, blok verebilseler bile geniş yüzeylerle üretilmeye ve parlatılmaya elverişli değildirler. Mermerler gibi parlak yüzeyli levhalar haline getirilemeyen bu taşların da önemli özellikleri bulunmaktadır. Bu özellikler; yumuşak ve homojen yapıları vardır, sertlik ve özellik değiştirmelerine neden olacak çatlak dolgular ve mineralli karmaşıklıklar içermezler, izotropik olduklarından, el aletleri ve bazı küçük cihazlarla, her yönde kolayca işlenebilir veya kesilebilirler, genellikle hafiftirler, nakledilmeleri, işlenmeleri ve işlenmişlerin montajı kolaydır, pahalı ve az bulunur olmadıklarından, çalışırken ortaya çıkan fire korkutucu bir faktör değildir. Birçoğu özellikle tüfler ve killi kireçtaşları, bazen de oolitikler, değişik göz alıcı renklere sahiptirler. Bina balkonlarında, görünür yüzeylerde, bazı sanat yapılarında, yerleri bulunmaz şekilde kullanılmaktadırlar. Ucuz, kolay işlenebilir ve genellikle renk açısından homojen olduklarından, aşınmış veya bozulmuş olanları yenisiyle kolaylıkla değiştirilebilir [1,2].
2. KANDIRA TAŞI
Literatürde çeşitli yazarlar tarafından volkanosedimanter kum taşı [3], volkanik tüf [1,4] ve biyomikritik kireç taşı [5,6] gibi kayaç gruplarına örnek gösterilen Kandıra taşı, gerek doğal dokusu, gerekse kullanıldığı ortamdaki dayanımı açısından cazip olmakta ve çeşitli alanlarda tercih edilmektedir. Bu çalışmalar içerisinde Kandıra taşı konusunda petrografik açıdan yapılan tek spesifik akademik sınıflandırma Tansel [5,6]’ e aittir, diğer tarifler literatürde genel kabul olarak bulunmaktadır. Dolayısıyla bu çalışmada, taşın biyomikritik kireç taşı sınıfında olduğu hipotez olarak kabul edilmiştir. Bileşiminde % 90’ dan fazla CaCO3 bulunan kayaçlara kimyasal veya biyokimyasal sedimanter (tortul) kayaçlar başlığı altında incelenen kireçtaşı (kalker) adı verilmektedir. Mikrit, 4 μm’ den küçük boyutlu CaCO3 kristallerine verilen isimdir. Mermer ile kalker arasındaki fark mermerin metamorfizma geçirmiş olmasıdır. İri kristaller ışığı çeşitli yönlerde yansıttıklarından mermerler gösterişlidir, küçük kristalli kalkerler ise parlamazlar. Mikritik olmayan kalkerler de bulunmaktadır. Kireçtaşları genellikle organizmaların, biyolojik işlevleriyle oluşmakta, denizel orijinli olmakta ve yapısında denizlerde yaşayan organizmaların (mikrofosiller) fosillerini bulundurmaktadırlar. Kireç taşları, fazla sert olmamaları, kolayca işlenebilmeleri, bol bulunmaları nedenleriyle hemen her türlü yapıda inşaat malzemesi olarak kullanılmaktadır [1,2].
Günümüzde, Kandıra taşının en çok kullanıldığı alan kesme veya dekoratif taşlar olarak da isimlendirilen yontma taşlar grubudur.Yontma taşlar, eski zamanlarda da kullanılmışlardır. En göz alıcı örnekleri, Selçuklular zamanında yapılan camiler, hamamlar, medreseler ve kümbetlerde görülmektedir. Aynı örnekler daha önceki tarihlerde, Ani şehri harabelerinde de kullanılmıştır. Osmanlılar döneminde, yine aynı tür yapılarda ve Ankara’ da Cumhuriyetten önce ve sonra yapıtaşlarından çok geniş şekilde yararlanılmıştır [1,2,7]. Kandıra taşı; tarihi ve günümüz yapılarında dış cephe/bahçe duvarı kaplamaları, parke taşı, barbekü, şömine veya bir heykel şeklinde yaygın kullanım alanı bulmaktadır. Kolay şekillendirilebilmesi, krem-sarı rengi ve dayanıklılığı sebepleriyle Kandıra taşının kullanımı sadece bu alanlarla sınırlı kalmamaktadır. Restorasyon diğer bir kullanım alanıdır. Marmara bölgesindeki bazı tarihi eserler Kandıra taşı ile restore edilmişlerdir. Kandıra taşı son olarak, ünlü iş adamı Vehbi Koç’ un, Çengel Han’ daki (İstanbul) ilk dükkanının restorasyonunda kullanılmıştır. Müze olarak kullanılacak mekanın pencere ve şömine kenarlarında Kandıra taşı kullanılmıştır [8]. Reintegrasyon (Bütünleme), bir bölümü hasar görmüş, yada yok olmuş yapının öğeleri ilk haline kavuşturulacak şekilde geleneksel malzeme ile veya zamanın şartlarına göre çağdaş malzeme ile bütünleme demektir. Bütünleme sonucu aşınmış ve yorulmuş malzemeler yerinden alınarak aslına uygun yeni malzemelerle değiştirilmektedir. İstanbul’ daki bazı yapılarda kullanılan Malta taşına en benzer malzeme Kandıra taşı dır. İtalya’ nın güneyinde bulunan Malta takım adalarında, denizden çıkartılan ve kimyasal yapısı sebebiyle çok kolay işlenebilen Malta taşının reintegrasyonunda da Kandıra taşı kullanılmaktadır [9].
3. DENEYSEL ÇALIŞMALAR
Basma mukavemeti deneyi, schmidt sertlik çekici deneyi, özgül ağırlık deneyi, su emme deneyi, sodyum sülfat don kaybı deneyi ve mikroyapı incelemeleri mekanik ve fiziksel deneyler olarak, rezidüel kil analizi deneyi ise kimyasal deney olarak seçilmiştir. Deneysel çalışmalar, Sakarya Üniversitesi laboratuarlarında uygulanmıştır [10-12]. Deneylerde kullanılan malzemeler, krem-bej renkli Kandıra taşıdır ve taş ocağının sınırlı bir bölgesinden alınmıştır. Farklı bölgelerdeki ocaklardan alınan numunelerin deneysel değerlerinin birbirinden farklı çıkabilme ihtimali göz önünde bulundurulmalıdır.
3.1. Basma Mukavemeti Deneyi
Endüstriyel uygulamalarda basma kuvvetlerinin uygulandığı yerlerde kullanılan malzemeler genellikle gevrek malzemelerdir. Tuğla, beton gibi malzemelerin basma mukavemetleri, çekme mukavemetlerinden çok daha yüksek olduğundan bu gibi malzemeler basma kuvvetlerinin uygulandığı yerlerde kullanılırlar ve özellikleri basma deneyi ile belirlenir.
Deneysel çalışmada, maksimum 200 ton basma kuvvetine ve Profi-2 dijital göstergeye sahip ALŞA marka basma deney cihazı kullanılmıştır. Basma deneyi için Kandıra taşının farklı ebatlarından 50x50x50 mm boyutlarında kare prizma şeklinde numuneler hazırlanmıştır. Deney TS 699’ a göre yapılmıştır [10]. Deneyde toplam 10 adet numune kullanılmış ve deney cihazından basma kuvveti (kg) cinsinden okunmuştur. Basma mukavemeti, basma kuvvetinin (P) örneğin orijinal kesit alanına (Ao) bölünmesiyle elde edilmektedir (Formül 1) [10,11]. Deney sonucunda elde edilen basma kuvvetleri ve Formül 1’ den hesaplanan basma mukavemeti değerleri Tablo 1’ de verilmektedir.
EMBED Equation.3 (kg/cm2) Formül (1)
Tablo 1. Basma deneyi sonucu elde edilen değerler
Numune | Basma Kuvveti (kg) | Basma Mukavemeti (kg/cm2) |
1 | 9690 | 387,6 |
2 | 8175 | 327 |
3 | 12100 | 484 |
4 | 10225 | 409 |
5 | 12640 | 505,6 |
6 | 9550 | 382 |
7 | 12970 | 518,8 |
8 | 8875 | 355 |
9 | 8900 | 356 |
10 | 9960 | 398,4 |
Minimum | 8175 | 327 |
Maksimum | 12970 | 518,8 |
Ortalama | 10308,5 | 412,3 |
Tablo 1’ den de görüldüğü üzere ortalama basma mukavemeti değeri 412,3 kg/cm2 olarak tespit edilmiştir. TS 11137’ de [13] verilen “Süs ve duvar kaplamasında kullanılacak kireçtaşları için tek eksenli basma mukavemeti değeri 300 kg/cm2 ‘den az olmamalıdır.” ibaresine göre bulunan değer, taşın kaplama işlemi için uygun olduğu anlamına gelmektedir. Bazı kayaçların basma mukavemetleri ise; bazalt 500 kg/cm2, kumtaşı 800 kg/cm2, granit-andezit 1200 kg/cm2 değerlerinden yüksek olmaktadır [14]. Bell ve Lindsay [15] çalışmalarında, kumtaşının basma mukavemetinin minimum 770 kg/cm2 ile maksimum 2140 kg/cm2 arasında ortalama ise 1366 kg/cm2 olduğunu belirtmektedirler. Şimşek [16], tuğla duvar için maksimum basma mukavemetini 85 kg/cm2, taş duvar için 50 kg/cm2 olarak belirtmiştir. TS 704’ e göre duvar yapımında kullanılan dolu ve delikli harman tuğlalarının basma mukavemeti orta dayanımlılar ve az dayanımlılar için sırasıyla minimum ortalama 50 kg/cm2, ve 30 kg/cm2 olmaktadır [17]. Dolu tuğlalarda basma mukavemeti 200 kg/cm2’ ye çıkabilmektedir. Yapı malzemesi olarak kullanılan kerpiç’ in basma mukavemeti, killi toprağın cinsine bağlı olarak 5-20 kg/cm2 arasında değişmektedir. İnşaat sektöründe yaygın olarak kullanılan BS 16, BS 20 ve BS 25 sınıfı normal dayanımlı betonların, eşdeğer küp basınç mukavemetlerini sırasıyla 200 kg/cm2, 250 kg/cm2 ve 300 kg/cm2 olarak verilmektedir [18].
3.2. Schmidt Sertlik Çekici Deneyi
Bu deney, Schmidt çekici kullanılarak, kayaçların geri sıçrama sertliğinin tayini ve dolaylı olarak tek eksenli sıkışma dayanımlarının saptanması amacıyla yapılmaktadır. Deney uygulamasında TS 699 ve kaya mekaniği laboratuar deneyleri kitabı referans alınmıştır [10,11]. Çekicin ucu deney yüzeyine dik konumda olacak şekilde yavaşça bastırılır ve çekicin içindeki yaydan geri tepme sesi geldiği anda, çekicin gövdesi üzerindeki gösterge sabitleme tuşuna basılarak geri sıçrama değeri çekicin gövdesindeki göstergeden okunur. Deney örneği üzerinde birbirinden uzaklığı en az çekicin uç çapına eşit olan, en az 10 farklı noktada tekrarlanan değerler kaydedilir. Bu değerler en büyükten en küçüğe doğru sıralanır ve en küçük % 50’ si iptal edilir, diğerlerinin ortalaması alınır [11]. Schmidt sertlik çekici deneyi için ölçülen değerler Tablo 2’ de verilmektedir.
Tablo 2. Schmidt sertlik çekici deneyi için ölçülen değerler
Örnekleme Derinliği (m) | Çekicin Konumu | Geri Sıçrama Sertlik Değerleri (N) | Ortalama (N) | Birim Hacim Ağırlığı (kN/m3) | Basma Muk. (MPa) |
Yüzey | Yatay | 33,35,35,37,37,38,38,40,40,40 | 39,2 | 26,4 | 49 |
Deney örneğinin dolaylı yoldan tek eksenli basma mukavemetinin saptanması için, örneğin birim hacim ağırlığı (γ=9,81 özgül ağırlık) ve schmidt sertlik değerleri, çekicin deney sırasındaki konumuyla birlikte dikkate alınarak Şekil 1’ de verilen grafikten belirlenir.
Şekil 1’ de yatay çekiç skalasında sertlik değeri olan 39,2 N ile birim hacim ağırlığı 26,4 kN/m3 değerleri yerine konduğunda basma mukavemeti değeri yaklaşık 490 kg/cm2 olarak okunmaktadır. Bu değer basma mukavemeti deneyinde elde edilen minimum ve maksimum mukavemet değerleri aralığında kalmaktadır. Schmidt deneyi, basma mukavemeti deneyinin doğruluğunu da göstermektedir. Bell ve Lindsay [15] çalışmalarında, kumtaşının ortalama 1366 kg/cm2 olan basma mukavemeti için schmidt sertlik değerini ortalama 44,1 N olarak tespit etmişlerdir.
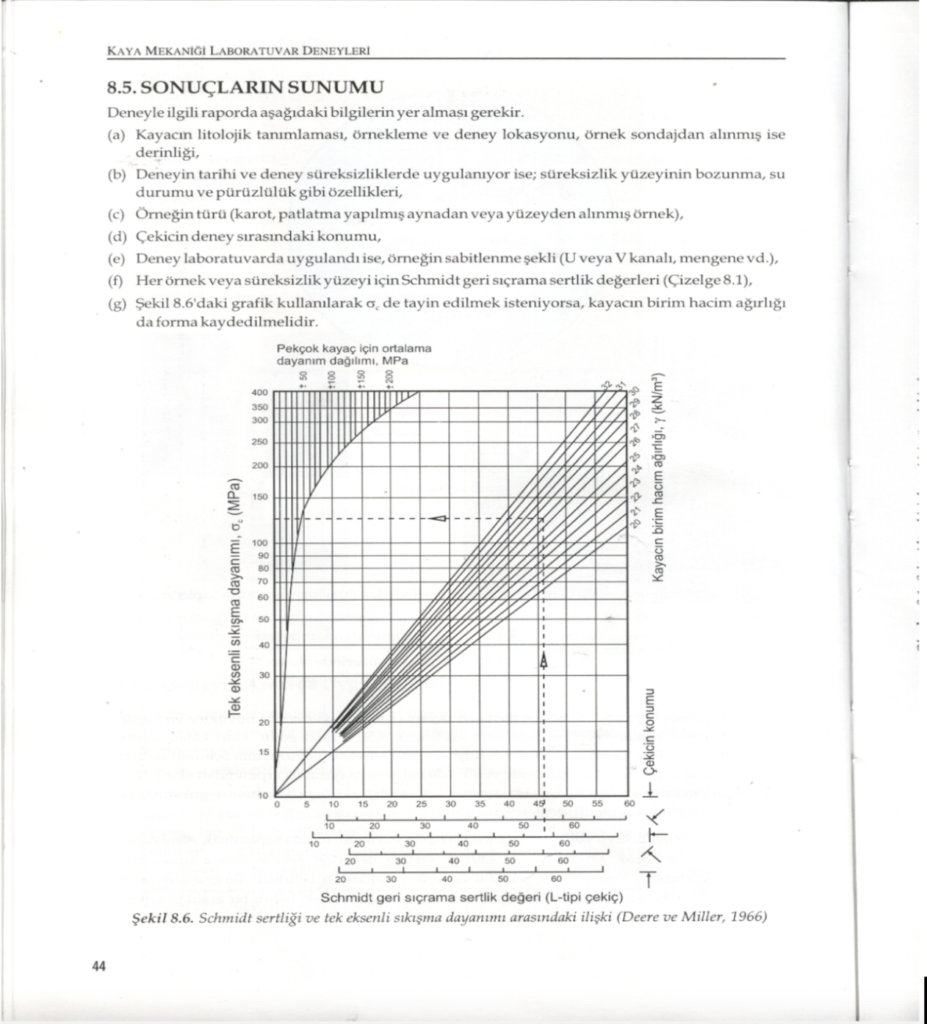
Şekil 1. Schmidt sertliği ve tek eksenli basma mukavemeti arasındaki ilişki [11]
3.3. Özgül Ağırlık Deneyi
Deney sırasında ağırlık tartımları, Avery Berkel marka hassas terazi, kurutma işlemleri FN 500 Nüve marka etüv kullanılarak yapılmıştır. Deney TS 699’ a göre yapılmıştır [10]. Kırılarak alınan numune göz açıklığı 0,2 mm olan kare gözlü elekten geçirilmiş ve değişmez ağırlığa gelinceye kadar kurutulmuştur. Kurutma işlemleri etüvde 105±5 0C sıcaklıkta 24 saat süre zarfında yapılmıştır. Oda sıcaklığındaki saf su ile tamamen doldurulan piknometre, kapağı kapatıldıktan ve üzerindeki su damlaları kuru bir bezle alındıktan sonra 0,01 g hassasiyetle tartıldı (Gps). Piknometre içindeki su tamamen boşaltıldıktan, etüvde kurutulup soğutulduktan sonra tekrar tartılmış ve piknometre (kapağı ile birlikte) ağırlığı bulunmuştur (Gp). Kurutulup soğutulmuş olan öğütülmüş numuneden yaklaşık 15-20 g kadar alınarak piknometre içine konulmuş ve kapağı ile birlikte 0,01 g hassasiyetle tartılmıştır (Gpn). İçinde deney numunesi bulunan piknometre, hacminin 1/4 üne kadar su ile doldurulmuş ve taneleri içerisinde hava kabarcıklarının kalmaması için vakum pompası kullanılarak hava alma işlemi, yapılmıştır. Hava alma işlemi sonunda piknometre su ile tamamen doldurulmuş, kapağı kapatılarak üzeri kurulanmış ve 0,01 g hassasiyetle tartılmıştır (Gpns). Özgül ağırlık (d) değeri Formül (2) kullanılarak hesaplamıştır.
(g/cm3) Formül (2)
Burada; d = Taşın özgül ağırlığı (g/cm3), Gpn = (piknometre + deney numunesi) ağırlığı (g), Gp = Piknometre ağırlığı (g), Gpns = (piknometre + deney numunesi + su) ağırlığı, Gps = Su ile dolu piknometre ağırlığı (g) dır. Deneyde ölçülen değerler Tablo 3’ de verilmiştir.
Tablo 3. Özgül ağırlık hesaplamasında kullanılan değerler
Num. No | Pik. Ağırlığı Gp (g) | Pik.+Numune Gpn (g) | Pik.+Num.+Su Gpns (g) | Pik.+Su Gps (g) | Özgül Ağırlık d (g/cm3) |
1 | 37,561 | 57,550 | 151,011 | 138,411 | 2,705 |
2 | 37,662 | 52,347 | 147,077 | 137,813 | 2,709 |
3 | 38,336 | 61,551 | 153,338 | 138,684 | 2,712 |
Ort. | 2, 709 |
Kandıra taşının, 3 ayrı numune alınarak, 3 ayrı piknometrede uygulanan deneyleri sonucunda özgül ağırlık değerlerinin ortalaması 2,709 g/cm3 olarak bulunmuştur. Bulunan değer, TS 11137’ de [13] belirtilen “kireçtaşının özgül ağırlığı 2,16 g/cm3 ‘den daha az olmamalıdır” ve yine literatürde verilen “yapı malzemesinin özgül ağırlığı 1,8 g/cm3 değerinden büyük olmalıdır” ile “kireçtaşının özgül ağırlığı 2,7 g/cm3 olmalıdır” tariflerini doğrulamaktadır [1]. Bell ve Lindsay [15] kumtaşının, özgül ağırlığının ortalama 2,68 g/cm3 olduğunu belirtmektedirler. Bu değer kireç taşının, kumtaşıyla benzer yoğunluğa sahip olduğunu göstermektedir. Betondaki çimentonun özgül ağırlığı 3,1 g/cm3 [16] olmakla beraber, kompozisyona bağlı olarak betonun özgül ağırlığı 1,8-2,4 g/cm3 arasında değişmektedir. Dolu harman tuğlası 1,8 g/cm3, düşey delikli harman tuğlası 1,4 g/cm3, dolu fabrika tuğlası 1,8 g/cm3, delikli düşey fabrika tuğlası 1-1,4 g/cm3 ve delikli yatay fabrika tuğlası 0,5-0,8 g/cm3 arasında özgül ağırlık değerlerine sahiptir [7].
3.4. Su Emme Deneyi
Su emme deneyinde, Precisa 1212 M SCS marka 0,0001 gr hassasiyete sahip analitik terazi, Genlab Mobs/68/SS/F marka 105±5 0C’ ye kadar ayarlanabilen etüv ve çeşitli büyüklükteki kaplar kullanılmıştır. Numuneler oda sıcaklığında içi damıtılmış su ile dolu bir kap içerisine yerleştirilmiştir. 24 saatin sonunda numuneler sudan çıkarılmış ve yüzeylerindeki kaba su alındıktan sonra hassas terazide tartılmıştır (ms). Doymuşluğa ulaşıldığında emilen toplam suyu belirlemek için numuneler, sudan çıkarılıp, 105±5 0C’ de 24 saat süresince kurutulmuş ve tartılmıştır (mk). Kuru ağırlık ile doymuş ağırlık arasındaki fark, doyma noktasındaki emilen su olarak tanımlanmaktadır. Suya doymuş numunenin ağırlığı (ms), 24 saat kurutulup, oda sıcaklığında soğutulan numunenin ağırlığı (mk) ve ağırlıkça su emme oranı (as), Formül (3)’ den hesaplanmıştır. Deney TS 704 ve TS 699’ a göre yapılmıştır [10, 17]. Bulunan değerler Tablo 4’ de verilmiştir.
Su emme oranı % (aS) = [ (ms – mk ) / mk ] . 100 (%) Formül (3)
Tablo 4. Kandıra taşının ağırlıkça su emme deneyi sonuçları
Numune | Yaş Ağırlık mS (g) | Kuru Ağırlık mk (g) | Su Emme Oranı aS (%) |
1 | 625 | 596 | 4,8 |
2 | 511 | 487 | 4,9 |
3 | 496 | 472 | 5,0 |
Ortalama (%) | 4,9 |
Kandıra taşında tespit edilen ağırlıkça ortalama su emme oranı (% 4,7), kiremitlerin su emme oranından düşüktür. Kireç taşlarında su emme dokusal özellikler ve taşın bileşimine giren maddelerin çeşidine göre değişmektedir. Sert taşlarda su emme oranı % 0-1, betonda % 1-8 arasındadır [16]. Andezitte % 0,7’ den küçük olmalıdır [14]. Mevcut inşaat malzemeleriyle kantitatif kıyaslama yapmak gerekirse, TS 572 standardında [19], geleneksel kiremitler için su emme oranı % 13’ den küçük olanlarının kullanıma uygun olduğu belirtilmektedir. Deneysel çalışmada, piyasada satılan bir harman tuğlasının ağırlıkça su emme oranı % 18,1 olarak ölçülmüştür. Tuğlalarda su emme oranı % 18’ den büyük olmamalıdır. Genellikle % 8-18 arasında değişmektedir [18].
3.5. Sodyum Sülfat (Na2SO4) Don Kaybı Deneyi
Don kaybı deneyinde, su emme deneyinde kullanılan hassas terazi ve etüv ile birlikte deney çözeltisi ve numune için uygun büyüklükte kaplar, 350 gr susuz sodyum sülfat tuzunun (Na2SO4) 1 litre su içinde çözülmesiyle hazırlanan sodyum sülfat çözeltisi kullanılmıştır. Sırasıyla 40–25mm arası (1000 g), 25–20mm arası (1000 g), 20–10mm arası (500 g), 10–5mm arası (100 g) numune elenir, 110 º C±5 º C sıcaklıkta değişmez ağırlığa kadar kurutulur ve tartılır (G1). Daha sonra 40–25mm, 20–10mm ve 10–5mm arası üç grup numune içinde sodyum sülfat çözeltisi bulunan kovaya daldırılır. Numune çözeltinin içinde bu halde 18 saat bekletilir. Daldırma süresinin sonunda, numuneler çözeltinin içinden çıkartılır ve en fazla 4 saat süresince 110 ºC±5 ºC’ de değişmez ağırlığa kadar kurutulur. Oda sıcaklığına gelinceye kadar soğutulur ve tekrar çözelti kovasına daldırılır. Daldırma ve çıkartarak kurutma işlemi toplam 5 kez tekrarlanır. 5. tekrarlamanın sonunda, kurutulup soğutulan numune, su ile yıkanır. Yıkama işlemi tamamlanınca, numune 110 ºC±5 ºC’ de değişmez ağırlığa kadar kurutulur. 40-25mm ve 25-20mm arasındaki numuneler 20mm açıklığa sahip elekten, 20-10mm arasındaki numuneler 10mm ve 10-5mm arasındaki numuneler 5mm açıklıklı elek kullanılarak elenir, elek üstünde kalan kısım tartılır (G2). Bu eleklerden geçen kısımlar don kaybı olarak belirtilmektedir. % Don kaybı oranı (ad), Formül (4) ile hesaplanmaktadır [11].
ad = [ (G1 – G2) / G1 ] .100 (%) Formül (4)
Bu şekilde her grup için bulunan don kaybı değerlerinden Formül (5) yardımıyla taşın toplam don kaybı hesaplanır :
adt = 0,5 ad1 + 0,3 ad2 + 0,2 ad3 (%) Formül (5)
Burada; adt=Taşın toplam sodyum sülfat don kaybı (%), ad1=40–20mm elekler arasındaki deney numunesinin don kaybı (%), ad2=20-10mm elekler arasındaki deney numunesinin don kaybı (%), ad3=10-5mm elekler arasındaki deney numunesinin don kaybı (%) dır. Deney TS 699’ a göre yapılmıştır [10]. Bulunan değerler Tablo 5’ de verilmiştir.
Tablo 5. Kandıra taşının don kaybı deneyi sonucu bulunan değerler
Numune | 40-20 mm elek arası | 20-10 mm elek arası | 10-5 mm elek arası |
G1 (g) | 93 | 466 | 1952 |
G2 (g) | 88 | 446 | 1890 |
ad (%) | 5,4 | 4,3 | 3,2 |
adt (%) | 4,6 |
Boşluklara giren su donunca hacmi artmaktadır. Girdiği porozitelerde –5 °C’ de 620 kg/cm2, -10 °C’ de 1140 kg/cm2 basınç meydana getirmektedir. Dolayısıyla don kaybı deneyi kullanım şartlarında önemlidir [18]. Doğal taşlar, yapı malzemesi olarak kullanılacak ise dona dayanım deneyleri sonucu bulunan toplam ağırlık azalmasının % 5’ den fazla olmaması gerekmektedir [7, 20].
3.6. Darbeli Aşınma (Los Angeles) Deneyi
Deneyde, 11 adet aşındırıcı çelik bilye kullanılmıştır. Deney standartlara göre uygulanmıştır [10, 21]. Çekiç ile kırılan taşlar, 20-12,5 mm (2500 g) ve 12,5-10 mm (2500 g) eleklerden elenerek 110 ± 5 °C sıcaklığa ayarlanmış etüvde değişmez ağırlığa gelinceye kadar kurutulur. Daha sonra numuneler tartılır (G0). 5000 g ± 10 g deney numunesi ve çelik bilyeler Los-Angeles aşındırma cihazı içerisine konularak 100 devir yaptırılır. 100 devir sonunda cihazdan çıkarılan deney numunesi parçalarının tümü göz açıklığı 1,6 mm olan kare gözlü elekten elenir gerekirse elek üzerinde kalan kısım yıkanır, değişmez ağırlığa kadar kurutulup soğutulduktan sonra l g hassasiyetle tartılır. Bundan sonra 1,6 mm’ lik elek üzerinde kalan ve geçen tüm malzeme, çelik bilyelerle birlikte tekrar Los Angeles aşındırma cihazı içerisine konulur ve 400 devir daha yaptırılır. Bu suretle toplam 500 devir yaptırılmış olur. Cihazdan çıkarılan deney numunesi yukarıda açıklandığı şekilde yine göz açıklığı 1,6
mm olan kare gözlü elekten elenir, elek üzerinde kalan kısım gerekirse yıkanır, kurutulur ve tartılır. Deney sonucunda 500 devir sonundaki aşınma kaybı (K0), Formül (6) kullanılarak hesaplanmaktadır.
K0 = [ (G0 – G500) / G0 ] .100 (%) Formül (6)
G500=Deney numunesinin 500 devir sonunda göz açıklığı 1,6 mm olan elek üzerinde kalan kısmının ağırlığıdır (g). G500=3,650 g olarak ölçülmüş, buna göre 500 devir sonundaki aşınma kaybı K0 = % 27 olarak tespit edilmiştir. ASTM C 131-89’ a göre aşınan kısmın % 35’ den küçük olmasının yeterli olduğu belirtilmektedir [22]. Yazıcı [23], agrega olarak kullanılacak kireçtaşı için Los Angeles aşınma kaybını % 27 olarak tespit etmiştir. Terzi [24], çalışmasında kullandığı kireçtaşının Los Angeles deneyi sonucu aşınma kaybının % 17 olarak literatürde geçtiğini belirtmektedir.
3.7. Kalıntı Kil Analizi
Bu deney taş malzemedeki kalıntı kil miktarını bulmak için uygulanmaktadır. Kimyasal olarak hidroklorik (HCI) asitle reaksiyonu aşağıda eşitlik (1)’ de verilmiştir. Taşta herhangi bir reaksiyon meydana gelmezse, taşın kireçtaşı olmadığı, karbonat dışı bir malzeme olduğu saptanmaktadır. Reaksiyon sonucu meydana gelen tortulaşma ve renge bakılarak tortul veya başkalaşmış taşın türü hakkında karar verilmektedir [7,25].
CaCO3 + 2HCl CaCl2 + H2O + CO2 Eşitlik (1)
Hidroklorik asit, kalsiyum karbonat (CaCO3) ile reaksiyona girerek çözeltiye geçmesini sağlamakta ve çözeltide çökelen kısım ise kil, silisyum dioksit (fosil parçaları) ve diğer çözülmeyen minerallerden oluşmaktadır.
Bu analiz için Kandıra taşı kırılıp öğütülerek 2 mm elekten elenmiştir. 24 saat 105 ± 5 °C sıcaklıkta kurutulup, soğutulmuş 2 mm elek altı numuneden, 10.042 g tartılarak HCl ile muamele edilmiş ve sonra süzgeç kağıdı kullanılarak süzülmüştür. Süzgeç kağıdında kalan malzeme 105 ± 5 °C sıcaklıkta 24 saat kurutulmuş, soğutulduktan sonra tartılmıştır. Tartılan malzeme 0,909 g gelmiştir. Bu, Kandıra taşının % 90,95’ inin kalsiyum karbonat (CaCO3)’ dan, % 9,05’ inin ise kil, silisyum dioksit (SiO2) ve diğer çözülmeyen minerallerden oluştuğu anlamına gelmektedir [1]. Bell ve Lindsay [15] kumtaşı konusunda yaptıkları çalışmalarında, kumtaşında maksimum % 10 kalsit, % 23’ den fazla kil ve ortalama % 59,2 SiO2 bulunduğunu ifade etmektedirler. Bu sonuç, Kandıra taşının bir kum taşı olmadığını ve kireç taşı sınıfında incelenmesinin doğru olduğunu ifade etmektedir.
3.8. Mikroyapı İncelemeleri
Kristal içyapısı düzenli bir katıdır. Atomların düzenli dizilişi sonucu bir kristal, düzgün dış yüzeyler oluşturmaktadır. Minerallerin çoğu, düzenli bir kristal yapıya ve belirli bir kimyasal bileşime sahiptir. Bunlar her bir mineralin fiziksel ve kimyasal özelliklerini belirlemektedir; sertlik ve özgül ağırlık gibi mineralin fiziksel özelliklerine bakılarak nasıl oluştuğu ortaya çıkartılabilmekte, renk ve dış görünüm özellikleri kullanılarak mineral tanımlanabilmektedir [26,27]. Malzemelerin mikroyapılarının incelenmesi, onun geçmişi ve bulunduğu durumu hakkında bilgi verdiği gibi, gelecekte bu malzemeye ne gibi işlemlerin uygulanabileceği hakkında da bilgi vermektedir. Mikroyapı incelemeleri, yeni malzemelerin geliştirilmesi, malzemenin iç yapısının incelenmesi, çeşitli malzeme kusurlarının veya hasarlarının nedenlerinin araştırılması için çok önemlidir. Numuneler önce sırasıyla 60-120-180-240-320-400-600-800 ve 1000 numaralı SiC zımparalar kullanılarak Buehler 2000 marka metalografi cihazında zımparalanmış daha sonra cihaza parlatma keçesi takılmış ve sırasıyla 5 μm ve 1 μm boyutlu Al2O3 partikülleri içeren solüsyon kullanılarak parlatılmıştır. Parlatılan numuneler, Olympus BH2-UMA model optik mikroskop kullanılarak, x50 ve x100 büyütmelerde incelenmiş ve mikroyapı fotoğrafları çekilmiştir (Şekil 2-4).
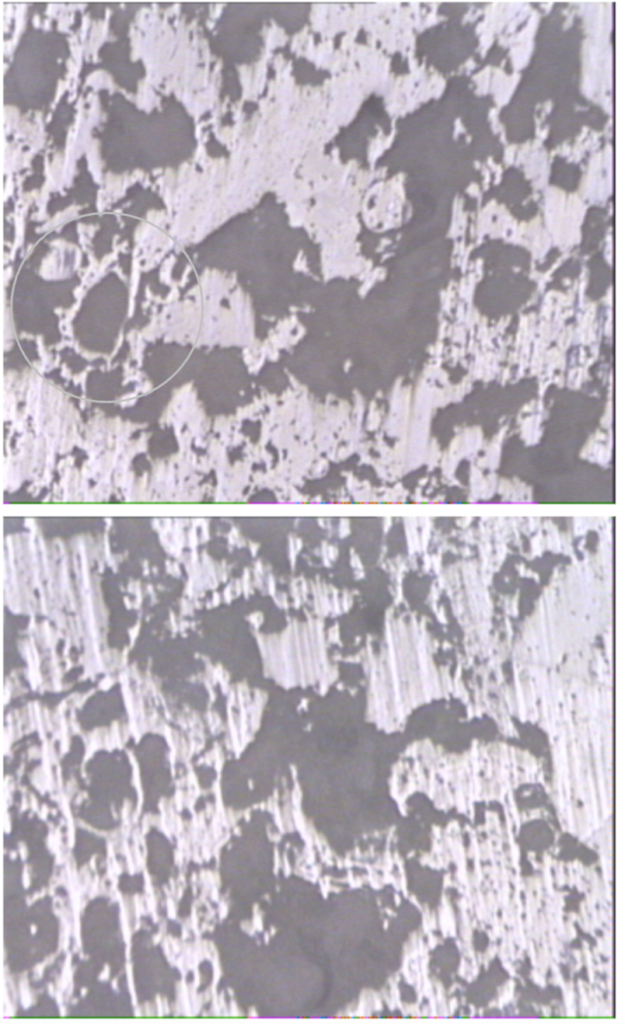
Şekil 2. Kandıra taşının mikroyapı fotoğrafları (x50)
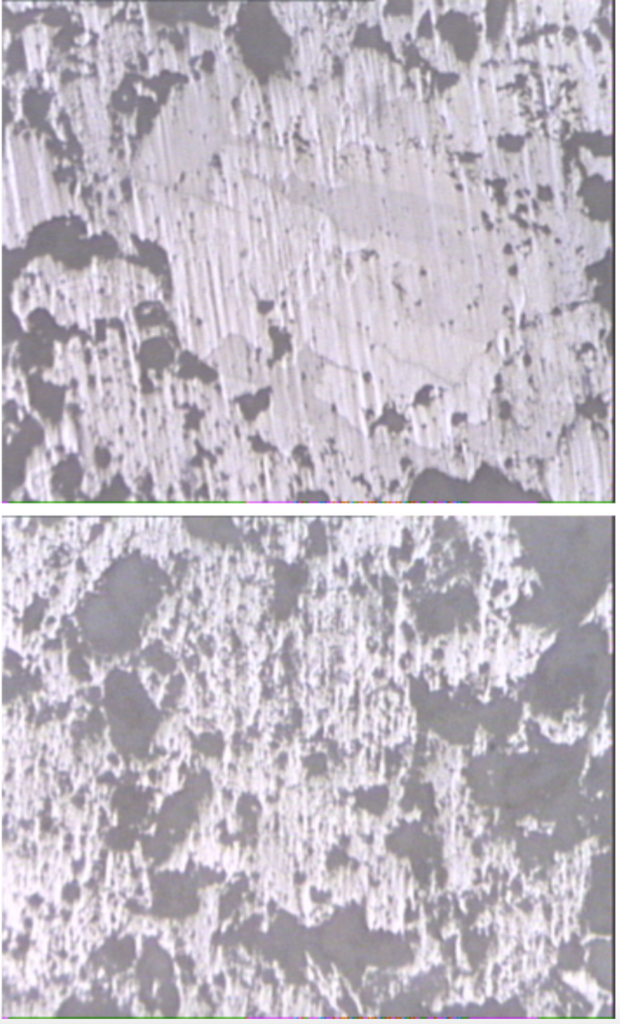
Şekil 3. Kandıra taşının mikroyapı fotoğrafları (x50)
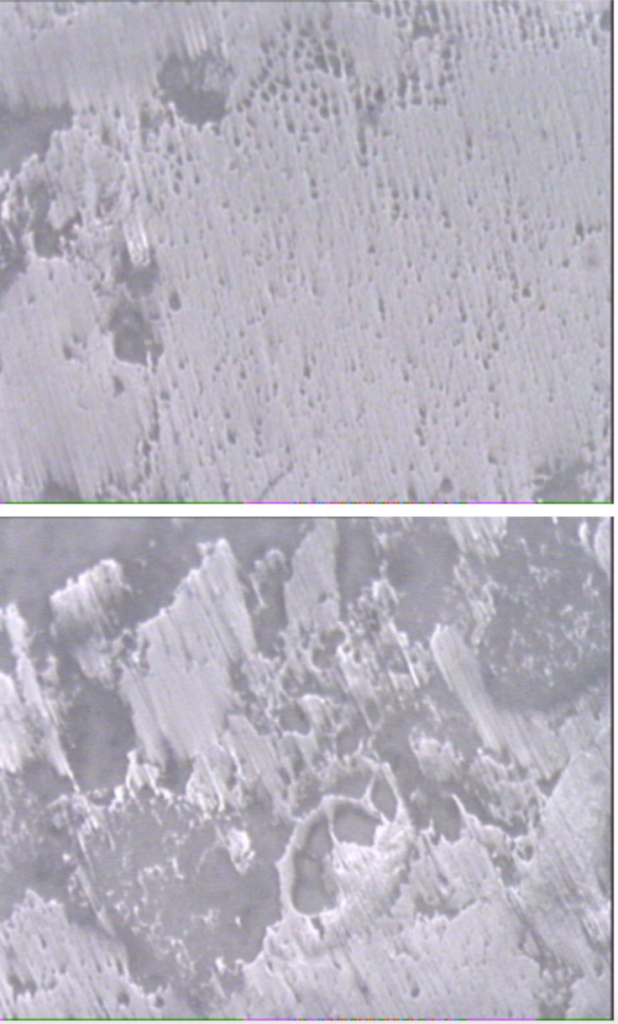
Şekil 4. Kandıra taşının mikroyapı fotoğrafları (x100)
Şekil 2-4’ deki mikroyapılar doğal taşlardan kireçtaşı yapısıdır [7]. Şekillerde siyah bölgeleri kil ve mikroporlar, gri bölgeleri ise CaCO3 teşkil etmektedir. Şekil 2 ve 4’ deki işaretli bölgelerde mikrofosiller görülmektedir. Yapı, büyük moleküller içinde atomların birbirine iyon bağları ile bağlanmaları sonucu oluşmakta, ancak serbest elektronlarının olmaması nedeniyle, ısı ve elektriği iletmemektedirler. İyon bağlarının kuvvetli oluşu malzemenin ergime noktasının yüksek olmasına neden olmaktadır. Yapılarındaki düzensizlik ve boşlukların bulunması sebebiyle gevrek yapılıdırlar, basma mukavemetleri, çekme mukavemetlerine göre yüksek olmaktadır.
SONUÇLAR
Büyük parça taşlardan deney numunelerinin çıkartılması sırasında numunelerin arayüzeylerinde, deneyler sırasında ve sonrasında ise kırık yüzeylerinde büyüteçle makroskobik incelemeler yapılmıştır. Yapıda, büyük ölçekte heterojenlik, renk değişimi ve büyük boyutlu porozitelerin varlığı gözlenmemiştir. Bununla birlikte, özelde koyu bej-kahve renkli kılcal damarlara nadiren rastlanılsa da, genelde taş tabii krem-bej rengini korumaktadır.
Mikroyapı incelemeleri sonucu, yapıda çeşitli deniz kabuklularının (fosillerin) varlığı gözlenmektedir. Bu kayacın biyolojik bir geçmişi olduğunun kayaç oluşumu sırasında çeşitli kabuklu deniz canlılarının yapıda yer aldığının bir göstergesidir. Bu canlıların kabukları genelde SiO2 bileşiklerinden oluşmaktadır. Rezidüel kil analizi sonuçlarına bakarak Kandıra taşının, kireç taşı (% 90,95 kalsit) yapısında olduğu söylenebilir. Kil, SiO2 ve diğer çözünmeyen minerallerin oranı ise % 9,05 olarak tespit edilmiştir. Dünyada ve Türkiye’ de gereğinden çok fazla kireçtaşı bulunmaktadır. Kireçtaşı anlatılırken onun rezervinden değil kalitesinden bahsetmek yerindedir. Kandıra taşı, bu kaliteyi yakalamıştır, gerek görünüşü gerekse dayanıklılığı kullanımını cazip kılmaktadır.
Kandıra taşı, basma deneyi sonucunda ortalama 412,3 kg/cm2 basma mukavemeti değerini vermiştir. Schmidt sertlik çekici deneyleri basma deneyine yakın mukavemet değeri vermiştir (490 kg/cm2). Bu sonuçlar ile malzemenin basma mukavemetini tanımlanmış olmaktadır. Özgül ağırlık deneyinden 2,7 g/cm3 değeri elde edilmiştir. Su emme deneyi ile taşın ağırlıkça su emme oranı % 4,9, sodyum sülfat çözeltisinde don kaybı % 4,6 olarak tespit edilmiştir. Los Angeles darbeli aşınma deneyinde, malzeme kaybı % 27 dir. Mohs sertliği açısından bakıldığında kalker yaklaşık 3 mohs sertlik değerindedir [1,26]. Kandıra taşı için bu değerin 2,5 mohs olduğu ifade edilmektedir [28].
Kandıra taşı, Kandıra’ nın sosyo-ekonomik gelişim sürecinde önemli bir doğal kaynaktır. Bölgede taş çıkartma ve işlemeciliğinden geçim sağlayanlar için vazgeçilmez bir gelir kaynağıdır. Yeni çevrelerin yapıları ve parkları hızla bu renge ve şekle donandığına göre Kandıra taşının yakın gelecekte çok daha yaygın şekilde kullanılacağı şimdiden söylenebilir. Heykeltraşlıkta, peyzaj mimarisinde, dekorasyonda ve restorasyonda kullanımının geliştirilmesinin yanı sıra taşın kullanım alanları bunlarla sınırlı kalmamalı yeni alanlar araştırılmalıdır. Birbirinden bağımsız küçük işletmeler tarafından yapılan taş çıkartma ve şekillendirme işlemleri organize, entegre ve çağın gerektirdiği ileri teknolojiler kullanılarak yapılmalıdır. Bu bakımdan, büyük olmayan sermayelerle çok iyi kuruluşlar doğabilecek ve çalışabilecektir. Maliyet analizleri, fizibilite çalışmaları yapılmalı, TSE ve ISO standardizasyonu uygulanarak kalite anlayışı getirilmelidir. Taşın yurtiçi ve yurtdışı tanıtımı daha aktif yapılmalıdır. Dünyaya henüz iyi tanıtılmamış bu taş potansiyelimizin önemli bir ihracat konusu olduğu da göz ardı edilmemelidir. Sonuç olarak yapılacak tüm faaliyetler, insana ve ekonomiye yatırımdır.
KAYNAKLAR
- ÖNLEM, Y.; “Sanayi Madenleri, Tanımları, Doğada Bulunuşları, Dünya ve Türkiye Rezervleri, Yıllık Üretimleri, İhraç ve İthal Miktarları”, Kozan Ofset, Ankara, Mart 1997
- ÜNSAL, N.; “İnşaat Mühendisleri için Jeoloji”, Gazi Üniversitesi, Mühendislik-Mimarlık Fakültesi, Ankara 2001
- YENER, L.; “Andezit Kullanımı ve Üretimi Üzerine Bir İnceleme”, http://www.topasgrup.com, 2004
- TEMUR, S.; “Endüstriyel Hammaddeler”, Çizgi Kitapevi Yayınları, No. 34, 3. baskı, s.342, Konya 2001
- TANSEL, İ.; “Ağva (İstanbul) Yöresinde Geç Kretase-Paleosen sınırı ve Paleosen Biyostratigrafisi”, TPJD Bülteni, C.1/3, s.211-228, Aralık 1989
- TANSEL, İ.; “Ağva (İstanbul ili) Yöresi Geç Kretase İstifinin Foaminifer Biyostratigrafisi”, Yerbilimcinin Sesi, sayı 17, Eylül 1989
- ERİÇ, M.; “Yapı Fiziği ve Malzemesi”, Literatür Yayınları, 2. Basım, İstanbul 2002
- “Vehbi Koç’un Dükkanı Müze Oluyor”, Kültür ve Sanat/Sergi, www.ntvmsnbc.com, 14.11.2004
- Es Yapı Şehircilik Mimarlık Restorasyon Ltd. Şti., http://www.esyapi.com, 01.11.2004
- TS 699; “Tabii Yapı Taşları – Muayene ve Deney Metotları”, Türk Standartları Enstitüsü, ICS 91.100.01;91.100.15, Ocak 1987
- ULUSAY, R., GÖKÇEOĞLU, C. ve BİNAL, A.; “Kaya Mekaniği Laboratuar Deneyleri”, TMMOB Jeoloji Mühendisleri Odası Yayınları, No. 58, Ankara, 2001
- CAMERON, E. N.; “Cevher Mikroskopisi”, İstanbul Teknik Üniversitesi Kütüphanesi, sayı. 811, İstanbul 1970
- TS 11137; “Kireçtaşı (Kalker) – Yapı ve Kaplama Taşı Olarak Kullanılan”, Türk Standartları Enstitüsü, UDK 552.54:691.215, Kasım1993
- ÖNENÇ, D. İ.; “Numune Alımı”, TMMOB, Jeoloji Müh. Odası, Teknik Tanıtım Serisi, http://www.jmo.org.tr
- BELL, F. G. and LINDSAY, P.; “The Petrographic and Geomechanical Properties of Some Sandstones from The Newspaper Member of The Natal Group near Durban, South Africa”, Engineering Geology 53, pp. 57-81, 1999
- ŞİMŞEK, O. “Yapı Malzemesi-I”, Ankara Üniversitesi Basımevi, Ankara 2001
- TS 704; “Harman Tuğlası (Duvarlar için), Türk Standartları Enstitüsü, UDK 621.421, Ocak 1979
- GÜNER, M. S. ve SÜME, V.; “Yapı Malzemesi ve Beton”, Bakanlar Matbaacılık Ltd. Şti, Erzurum 1999
- TS 562; “Oluklu Kiremitler ve Mahya Kiremitleri”, Türk Standartları Enstitüsü, UDK 691.424, Ekim 1986
- TS 1910; “Kaplama Olarak Kullanılan Doğal Taşlar”, Türk Standartları Enstitüsü, ICS 73.080-91.100.15, Şubat 1977
- TS EN 1097-2; “Agregaların Mekanik ve Fiziksel Özellikleri için Deneyler Bölüm 2: Parçalanma Direncinin Tayini için Metotlar “,ICS 91.100.15, Nisan 2000
- ASTM C 131-89; “Test Method for Resistance to Degradation of Small-Size Coarse Aggregates by Abrasion and Impact in the Los Angeles Machine”, The American Society for Testing and Materials Standards, 1992
- YAZICI, Ş.; “Değişik Akışkanlaştırıcıların Betondaki Performansları”, Denizli Üniversitesi, Mühendislik Fakültesi, Fen ve Mühendislik Dergisi, Cilt: 4, Sayı: 2, s. 41-52, Mayıs 2002
- TERZİ, S.; “Mermer Atıklarının Asfalt Betonu Karışımında Filler Malzemesi Olarak Kullanımı”, Yüksek Lisans Tezi, Süleyman Demirel Üniversitesi, Fen Bilimleri Enstitüsü, Isparta 2000
- OSTROM, E. M.; “Seperation of Clay Minerals From Carbonate Rocks by Using Acid”, Journal of Sedimantary Petrology 31, pp. 123-129, 1961
- SYMES, R. F.; “Taşların Dünyası”, Popüler Bilim Kitapları, TÜBİTAK, Kasım 2002
- KUŞCU, M.; “Endüstriyel Kayaçlar ve Mineraller”, Süleyman Demirel Üniversitesi Yayınları, No. 10, Isparta, 2001
“Hardness (Mohs) of Kandira Beige”, Marmer Producten, http://www.geocities.com/simextr/nedmer.html, 2004